설계 소프트웨어(CAD, 시뮬레이션, EDA): SaaS의 유일한 해자
소프트웨어 역사를 돌아보면, 거의 모든 소프트웨어 카테고리가 기술 변화에 따라 신생 기업들이 등장해 기존 기업들을 밀어내는 파도를 겪었다는 것을 알 수 있습니다. 이러한 변화 중 많은 부분이 클라우드를 통해 이루어졌습니다. 클라우드는 소프트웨어 개발에 대한 진입 장벽을 근본적으로 낮췄습니다. 이제 기업들은 데이터 센터 대신 신용카드만으로 소프트웨어를 구축할 수 있게 되었습니다. 거의 모든 소프트웨어 산업에서 "클라우드 네이티브" 기업들이 등장해 기존 기업들과 경쟁하게 되었습니다.
하지만 한 가지 산업이 예외로 두드러집니다: 바로 물리적 설계 소프트웨어입니다.
CAD, EDA, 그리고 시뮬레이션 제공업체들은 이제 그 어느 때보다도 더 강력한 지배력을 보이고 있습니다.
이 글에서는 물리적 설계 소프트웨어의 역사를 살펴보고, 리더들이 오랜 시간 동안 어떻게 지배력을 유지했는지, 현재의 기술과 시장에 대한 개요, 그리고 이 산업의 미래가 어떻게 될 수 있는지에 대한 견해를 제시하겠습니다.
본격적인 논의에 앞서, 현재의 물리적 설계 프로세스에 대한 개요를 간략하게 살펴보겠습니다. 자세한 내용은 뒤에서 다룰 예정입니다:
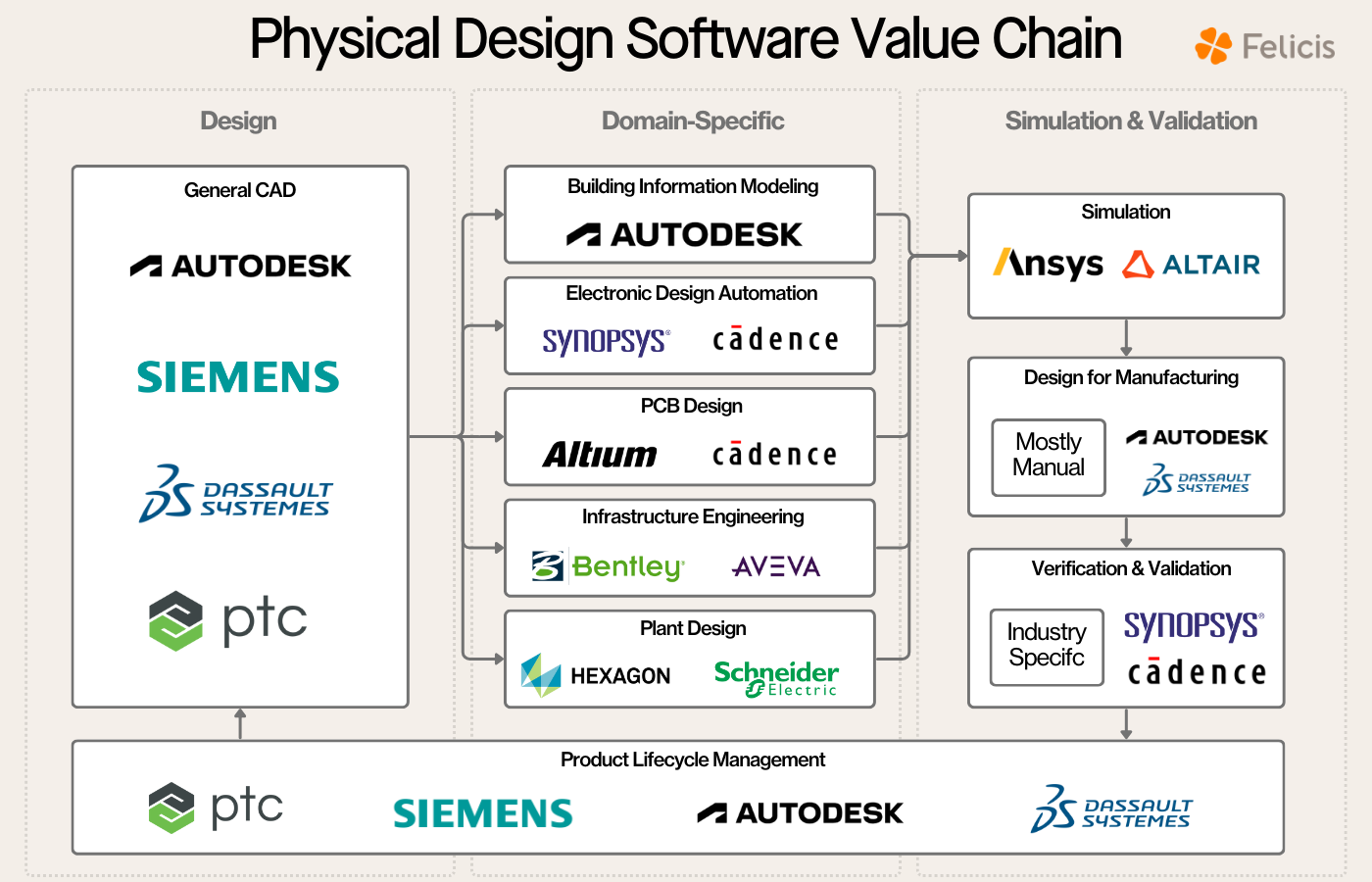
물리적 설계 소프트웨어의 역사
물리적 설계 소프트웨어의 역사는 크게 업계의 초기 역사와 '현대적' 설계 회사의 등장으로 나눌 수 있습니다.이 섹션의 대부분은 Shapr3D의 "엔지니어링 설계 혁명-CAD의 역사"에서 정보를 얻었습니다.
이 섹션의 많은 부분은 Shapr3D에서 제공한 "The Engineering Design Revolution—A History of CAD"에서 참고했습니다.
설계 소프트웨어의 초기 역사
1960년대 이전에는 물리적 시스템이 수작업으로 설계되고 도면화되었습니다.
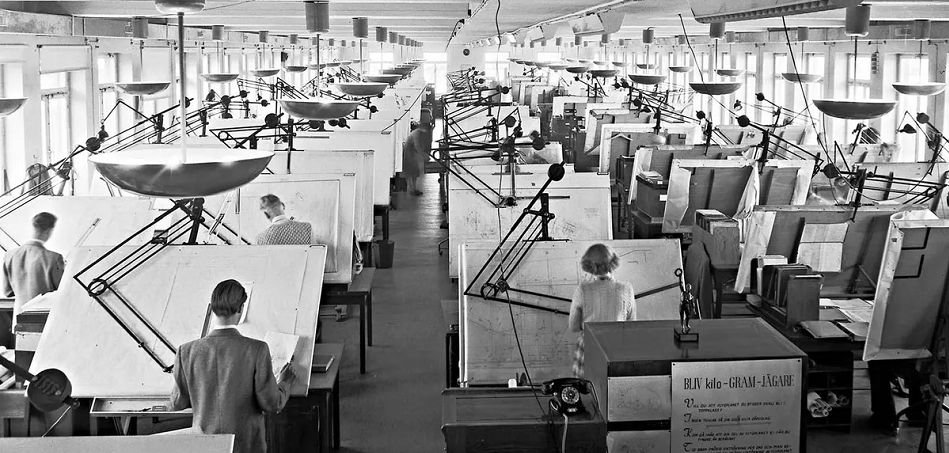
많은 기술 트렌드와 마찬가지로, CAD 산업은 대기업 내에서 시작되었습니다. 1957년, 패트릭 해너티(종종 CAD의 아버지라 불림)는 GM 연구소에서 컴퓨터로 자동화된 설계(Design Automated by Computer, DAC)를 만들었습니다. 1960년대 중반까지 대형 제조업체들은 컴퓨터 기반 설계의 가치를 인식하기 시작했습니다. 특히 자동차 회사들, 예를 들어 르노와 포드는 복잡한 표면을 수학적으로 모델링하는 데 집중했습니다. 르노 시스템은 오늘날 주요 일반 CAD 회사 중 하나인 Dassault Systemes가 되었습니다.
그러나 곧, Applicon, ComputerVision, Auto-trol, Calma, M&S Computing(후에 Integraph로 알려짐)이라는 다섯 개 주요 회사에서 최초의 상업 시스템이 등장하게 됩니다. 이 회사들은 주로 하드웨어 제조업체였으며, 하드웨어 판매를 촉진하기 위해 소프트웨어를 개발했습니다. 1972년에는 각 기계가 약 15만 달러에 판매되었습니다. Ansys도 이 시기에 설립되어 엔지니어링 시나리오를 시뮬레이션하기 시작했습니다.
이 5개 회사의 과점은 워크스테이션과 PC의 등장까지 계속해서 강화되었습니다.
“현대” 설계 소프트웨어의 등장
1980년대는 기존 과점을 뒤흔들고 향후 (달력 확인) 40년 동안 산업 구조를 고정시켰습니다.
10년 초에, 각 기계의 비용은 약 30만 달러였고 CAD 엔지니어들이 이를 운영했습니다. Apollo와 같은 회사들에서 나오는 엔지니어링 워크스테이션의 등장은 하드웨어와 소프트웨어의 분리를 가져왔습니다. 이후 PC도 출시되었지만, CAD 소프트웨어를 지원하기에 PC 반도체의 성능이 충분해지기까지는 시간이 걸렸습니다. 이는 초기 소프트웨어 회사들이 하드웨어 개발에 신경 쓰지 않고 소프트웨어만 개발할 수 있는 문을 열어주었습니다.
1981년에서 1986년 사이, 오늘날 과점을 형성하는 설계 회사들 중 6개가 설립되었습니다: Mentor Graphics(1981), Autodesk(1982), Cadence(1983), Bentley Systems(1984), PTC(1985), Synopsys(1986). 이 회사들은 워크스테이션 및/또는 PC를 위한 설계 소프트웨어를 제작하여 기존 기업들보다 저렴하고 유연한 대안을 제시했습니다.
PC CAD 판매업체들은 또 하나의 기발한 전략을 채택했습니다 Clay Christensen 교수가 자랑스러워할 만한 전략):
CAD 기능의 80%를 비용의 20%에 판매하고, 소프트웨어만 판매하며, 하드웨어와 교육 서비스를 제공하는 "채널 파트너"에게 판매를 아웃소싱합니다.
이로 인해 기존 기업들이 따라잡을 수 없는 근본적인 파괴적 비즈니스 프로필이 만들어졌습니다.
1990년대 중반부터 오늘날까지 산업은 인수 합병과 제품 확장을 통해 통합되었습니다. 일반 CAD 제공업체는 현재 Autodesk, Dassault, PTC, Siemens(2000년대 인수를 통해 형성된 CAD/PLM 부문)를 포함한 4개 회사의 과점 구조를 이루고 있습니다. EDA 제공업체들은 Synopsys, Cadence, Siemens EDA로 통합되었습니다. Synopsys가 Ansys를 인수하면서 이 산업은 더욱 통합될 것입니다.
이 역사적 끝맺음이 다소 갑작스럽게 느껴진다면, 그것은 실제로 그러하기 때문입니다. 이 산업은 1980년대 이후로 큰 변화를 겪지 않았습니다. 회사들은 가격 모델을 변경하고 제품의 클라우드 기반 버전으로 전환하기 시작했지만, 산업 구조는 대체로 변하지 않았습니다.
이로 인해 우리는 과점 산업에 처하게 되었으며, “이것이 바뀔 가능성이 있는지, 그리고 그 변화를 이끌어내기 위해 무엇이 필요할지”를 물어야 할 시점에 도달했습니다.
왜 이러한 회사들은 붕괴되지 않았을까요?
이 산업을 이끄는 가장 흥미로운 질문, 즉 파괴가 부족한 이유에 대해 한 발짝 물러서서 답할 필요가 있습니다. 답은 소프트웨어 해자가 어떻게 생겼는지를 보여주는 사례 연구라 할 수 있습니다. 여기에 네 가지 주요 원동력이 있습니다:
- 기술적 복잡성: 이 소프트웨어들은 세계에서 가장 복잡한 소프트웨어 중 일부입니다. 예를 들어 EDA 소프트웨어는 도구마다 수백만 줄의 코드가 있습니다. 스타트업이 CAD 플랫폼과 기능적 동등성을 달성하기 위해서만 5년 이상의 시간을 소비할 수 있습니다. 따라서 이러한 도구를 기존만큼 잘 만드는 것도 어려운 일이지만, 더 나은 도구를 만드는 것은 더더욱 어렵습니다.
- 전환 비용과 위험: 기업들이 수십 년간 쌓아온 지적 재산권을 옮기고 직원을 재교육할 위험을 감수할까요? 소프트웨어의 복잡성 때문에 도구를 변경하는 데 상당한 재교육 시간이 필요하며, 이는 곧 생산성 저하와 잠재적 다운타임을 의미합니다. 게다가 설계 결함이 소프트웨어 전환으로 인해 발생할 경우, 그 비용은 소프트웨어 결함보다 훨씬 큽니다.
- GTM 문제: 대부분의 포춘 100대 하드웨어 및 인접 기업들은 이러한 도구를 사용하며, 이동할 이유가 거의 없습니다. 중견기업과 SMB들은 학교에서 가르치는 표준인 Autodesk를 사용하며, 엔지니어들은 그것에 익숙해지기 위해 몇 년을 소비합니다. 이는 산업의 표준입니다. 대규모 소비자 사용 사례는 거의 없기 때문에 시장의 하단부는 큰 가치를 제공하지 않습니다. 이는 기업이 판매를 시작할 만한 좋은 장소가 없음을 의미합니다.
- 하드웨어 엔지니어 ≠ 소프트웨어 엔지니어: 하드웨어 엔지니어들은 CAD, 시뮬레이션 및 모델링 플랫폼과 같은 가장 비싼 소프트웨어 라이선스를 보유하고 있지만, 도구 변경을 주도할 구매력을 갖고 있지는 않습니다. 하드웨어 조직 내의 문화와 프로세스는 소프트웨어와 크게 달라 새로운 기술을 흡수하는 속도가 느리며, 신제품을 위한 하향식 GTM이 어렵습니다.
이 모든 요소들은 소프트웨어 비즈니스의 "관성"으로 이어지며, 기업이 소프트웨어 제품을 변경하기 위해서는 대체 제품이 몇 배 더 나아야 한다는 것을 의미합니다. 현재까지는 기업이 대규모로 핵심 소프트웨어 스택을 교체할 만큼의 큰 성능 향상을 보지 못했습니다.
물리적 설계 프로세스 개요
물리적 설계 소프트웨어 산업의 진화는 소수의 지배적 플레이어들 중심으로 통합되는 것이 특징입니다. 지난 40년 동안 Autodesk, Cadence, Synopsys와 같은 회사들은 기술적 역량을 확장하고 경쟁사를 전략적으로 인수함으로써 시장 지위를 강화해 왔습니다.
다음은 물리적 설계 프로세스의 모든 단계를 설명한 이미지입니다:
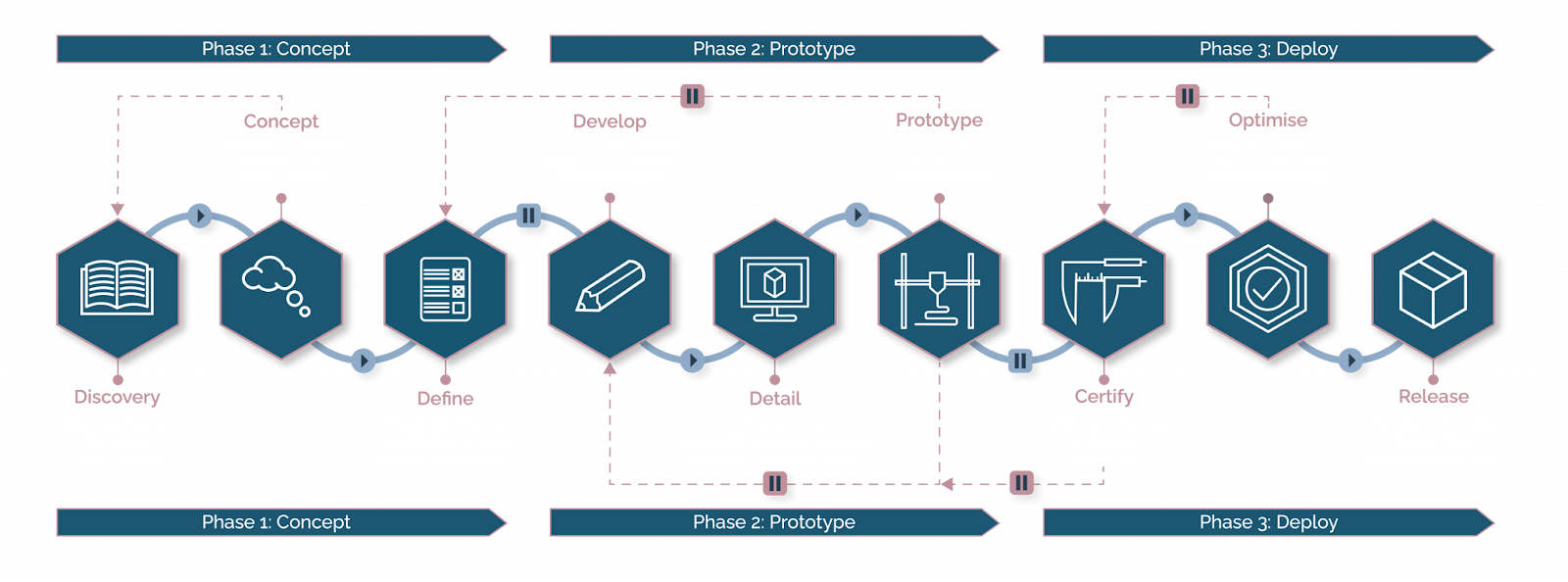
- 요구 사항 수집 및 개념 설계
설계의 첫 번째 단계는 내부 이해 관계자, 공급업체 및 고객으로부터 요구 사항을 수집하는 것입니다. 프로젝트 관리자는 이 모든 사람들과의 상호 작용을 조정하고 설계/구성 요소가 사양에 따라 개발되고 있는지 확인합니다.그러고 나서 산업 디자이너가 개념 설계를 만들고 이해 관계자로부터 피드백을 받아 이를 수정한 후 엔지니어링 팀에 전달합니다. 이 단계에서는 주로 Autodesk Alias나 Rhino3D와 같은 표면 모델링 도구를 사용합니다. - 세부 설계
엔지니어링 팀은 요구 사항을 참조하여 실제 구성 요소/시스템 설계를 시작합니다. 시스템 설계("X 크기의 엔진이 필요합니다")에서 하위 시스템 설계("실린더가 X개 필요합니다"), 그리고 구성 요소 설계(실린더를 구성하는 부품들)로 단계가 진행됩니다. 기계 시스템의 경우 일반 CAD 도구를 사용하게 됩니다.그러나 많은 산업에서 도메인 특화 설계 도구가 필요합니다. 몇 가지 예로는 칩 설계를 위한 EDA 도구, 회로 기판을 위한 PCB 도구, 건축을 위한 BIM 도구, 도로/교량/터널/수도 시스템 설계, 제조 플랜트 설계 도구가 있습니다. - 시뮬레이션
시스템이 세부적으로 설계된 후, 실제 시나리오에 최대한 가깝게 시스템을 시뮬레이션해야 합니다. 여기에는 하중 테스트를 위한 유한 요소 분석과 유체/가스 흐름을 위한 전산 유체 역학과 같은 기술이 포함됩니다. 실패가 발생하면 다시 설계하고 재테스트해야 합니다. Ansys는 이 분야의 선두 주자입니다. - 제조를 위한 설계 및 검증
기본적으로 3D CAD 도구는 현존하는 모든 형상을 만들 수 있습니다. 하지만 현존하는 모든 형상을 제조할 수는 없습니다. DFM은 사용 가능한 재료는 무엇인지, 대량 생산이 가능한지, 금속이어야 하는지, 모양을 단순화할 수 있는지, 사출 성형 또는 주조 중 어떤 방식으로 제조할 것인지 등 각 제조 단계가 가능한지 분석하는 과정입니다.
검증은 칩 설계에서 특히 중요한 최종 테스트 단계입니다. 칩/제품의 실제 성능은 가능한 한 철저하게 테스트해야 하며, 제조 결함이 발생하면 수백만 달러의 낭비가 발생할 수 있습니다. 결함이 발견되면 원인 분석을 거쳐 수정하고 다시 테스트해야 합니다.
이 단계는 현재 설계 프로세스에서 가장 수동적인 단계입니다. 대형 프로젝트의 경우, 이 단계에서는 경험이 풍부한 디자이너가 필요합니다.
프로젝트 수명 주기 관리
PLM 도구는 이 과정에서 백엔드의 데이터와 구성 요소를 관리합니다. 첫 번째 부분은 트리 형식으로 부품을 관리하고 각 시스템에 어떤 구성 요소가 있는지 및 모든 프로세스의 변화를 추적하는 것입니다. 두 번째 부분은 CAD 파일, 자재 명세서 및 버전 제어와 같은 데이터를 관리하는 프로젝트 데이터 관리입니다.
이 시장의 세그먼트를 일반 CAD 제공업체, 도메인 특화 제공업체, 그리고 도전 업체로 나눌 수 있습니다.
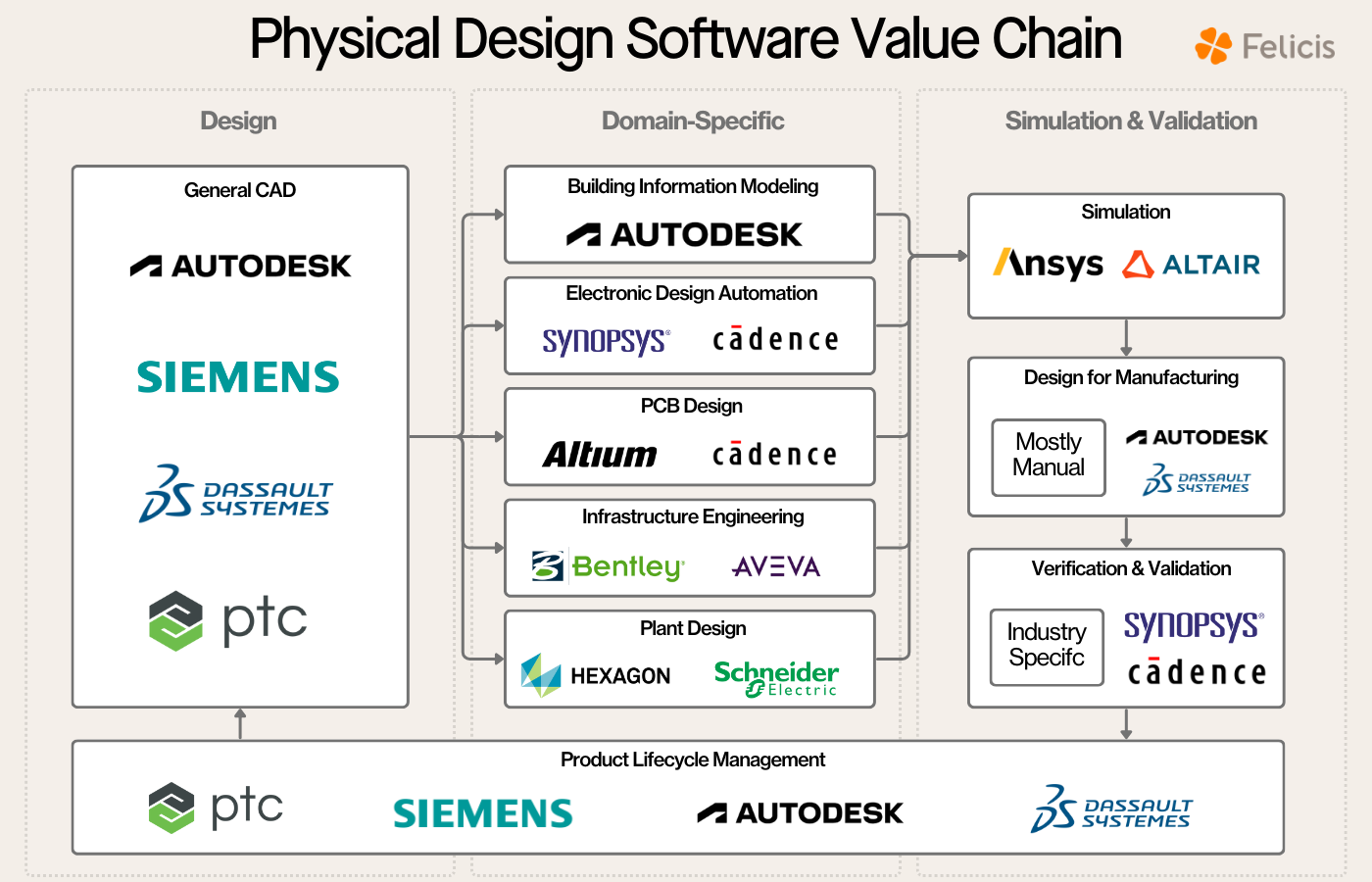
CAD 과점: Autodesk, Dassault, Siemens, PTC
이 네 회사는 각각 다른 시장 세그먼트와 수직적 초점을 가지고 비슷한 범위의 제품을 제공합니다. 이들 모두는 CAD, PLM, 그리고 다양한 설계 소프트웨어를 제공합니다.
Autodesk는 AutoCAD로 시작해 개인 사용자 중심으로 접근하였으며, 현재까지 그 위치를 유지하고 있습니다. 이들의 주요 비즈니스는 건축, 엔지니어링, 건설 "AEC" 산업에서의 BIM 소프트웨어(Revit, AutoCAD Civil)로, 이 부문 매출은 CAD 비즈니스의 두 배에 이릅니다. Autodesk는 CAD 소프트웨어(예: AutoCAD, Inventor)에서 중견기업과 SMB 시장을 지배하고 있습니다. 또한 PCB 설계, 건설 프로젝트 관리 소프트웨어, 수도 시스템 설계, 건설 급여 및 입찰 관리 등 놀라운 범위의 제품을 제공하며, 엔지니어링과 건설 소프트웨어 및 설계 소프트웨어에서의 확장을 지속하고 있습니다.
Dassault는 네 플레이어 중 가장 오래된 회사로, 성장 속도는 가장 느립니다. 이들의 초기 틈새 시장은 자동차 및 항공우주 회사들이었으며, 현재도 이 분야에서 시장 리더 자리를 지키고 있습니다. 이들의 기업용 제품은 CATIA이며, 중견기업용 제품은 Solidworks로, 업계 표준입니다. Solidworks는 학생들과 대학에서 가장 인기 있는 CAD 플랫폼입니다.
Siemens는 거대한 산업 회사로, 산업 소프트웨어 비즈니스를 계속 성장시켜왔습니다. 이들은 제조 라인을 위한 컴퓨터(PLC)와의 통합을 통해 하드웨어/소프트웨어 통합 및 배포 네트워크에서의 이점을 확보하고 있습니다. Siemens NX 소프트웨어는 Apple과 SpaceX와 같은 기업들이 사용하는 기업용 CAD 제품이며, Solid Edge는 중견기업용 제품입니다. Siemens는 네 회사 중 PLM 사업 부문에서 가장 큰 규모를 자랑하며, 다른 제공업체의 CAD와 함께 Siemens의 PLM이 사용되는 경우가 많습니다.
마지막으로, PTC는 네 회사 중 가장 규모가 작습니다. 이 회사는 제조 부문에 초점을 맞추고 있으며, 2010년대에 AR/VR과 공장 분석을 플랫폼에 통합하려는 시도를 했습니다. 이러한 노력은 큰 성공을 거두지 못했으며, 아마도 기술이 준비되기 전에 너무 일찍 인수한 결과일 가능성이 큽니다.
이들의 시장 세분화는 다음과 같이 나타납니다:
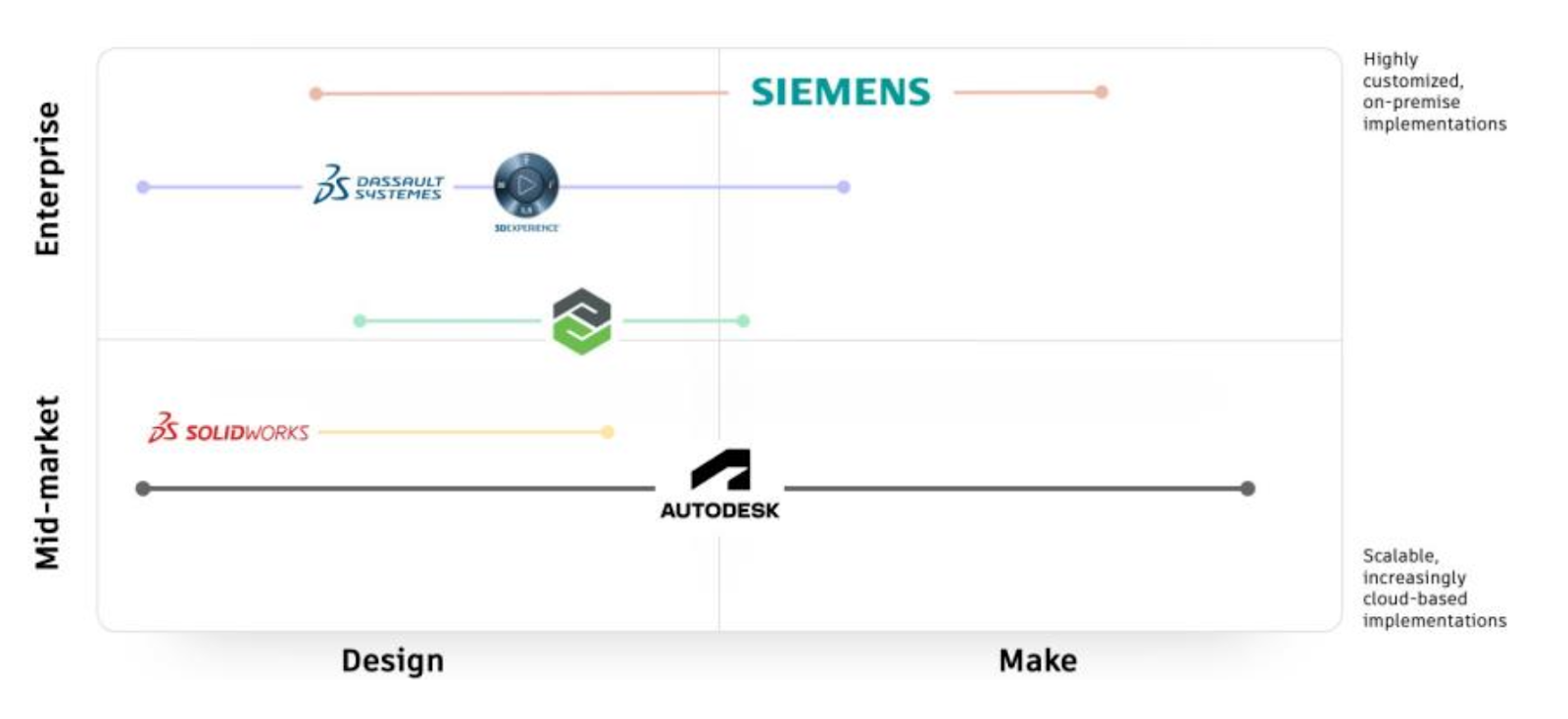
도메인 특화 CAD 소프트웨어
이의 가장 좋은 예는 칩 설계를 위한 EDA 소프트웨어로, Synopsys와 Cadence는 세계에서 가장 높은 가치를 지닌 소프트웨어 회사들 중 두 곳입니다. 많은 투자자들이 새로운 칩 설계 비용이 기하급수적으로 증가하는 것을 한탄하지만, 우리는 칩 설계 비용 증가가 성능 향상과 함께 둔화된 것을 목격했습니다. 칩 설계에서 가장 흥미로운 트렌드 중 하나는 반도체의 수직화, 칩렛, 패키징입니다. 무공장 모델이 지속되면서 더 많은 조직들이 맞춤형 칩을 요구하는 것을 볼 수 있습니다. AI와 자동화가 칩 설계 소프트웨어에서 수년간 사용되어 왔지만(예: 배치 및 라우팅), 우리는 기존 업체들이 여기서 막대한 데이터 이점을 가지고 있다고 생각하며, 스타트업들은 IP 문제를 피하기 위해 매우 창의적인 데이터 포지셔닝을 해야 할 것입니다.
다음은 EDA 제품 세그먼트와 각 세그먼트의 시장 리더에 대한 개요입니다:
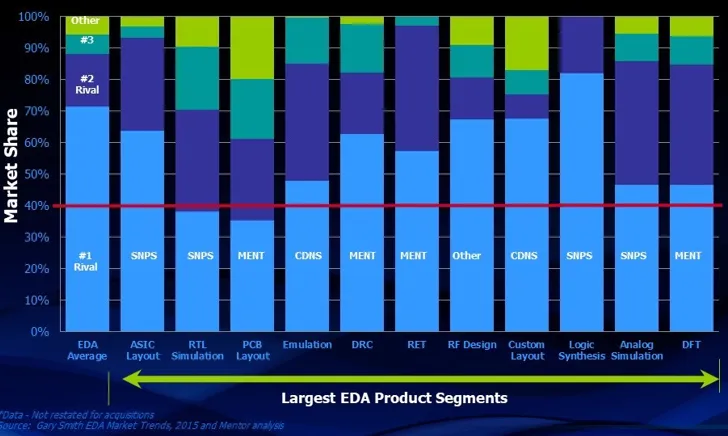
또 다른 예로는 도로, 교량, 터널, 플랜트와 같은 인프라 엔지니어링 도구가 있습니다. Bentley Systems는 OpenRoad, OpenBridge, OpenRail과 같은 프로젝트를 설계하는데 사용되는 이 분야의 시장 리더입니다. 이 회사는 이 분야에서 사실상 표준으로 자리 잡고 있으며, 50개 미국 주 중 48개 주에서 Bentley 제품을 사용한다고 알려져 있습니다. 플랜트 설계에서는 Hexagon, Schneider Electric, Bentley가 이 제품들에 대한 솔루션을 제공합니다.
도전 업체
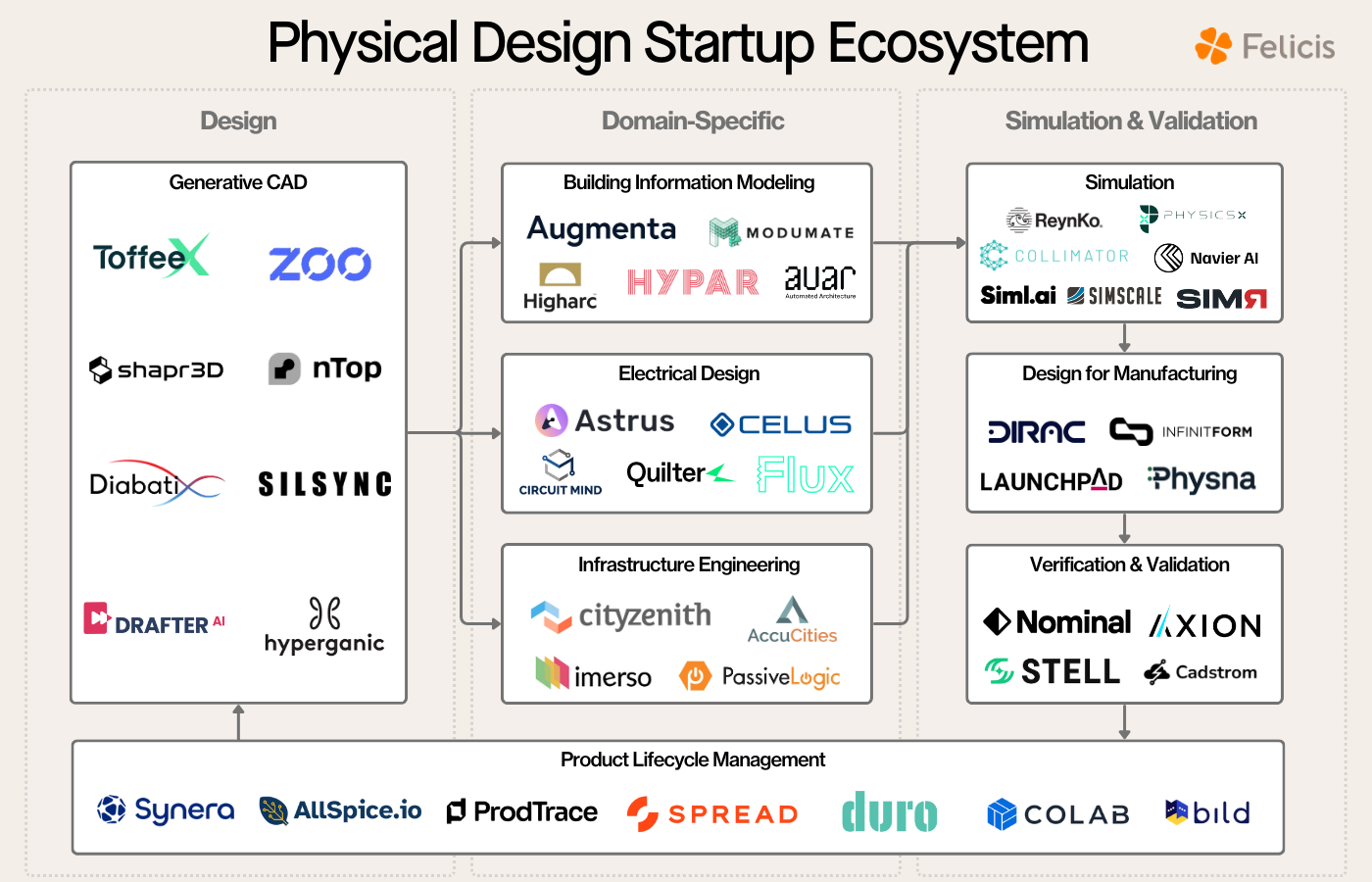
어떤 스타트업도 CAD 회사의 상위 계층에 진입하지 못했고(아직까지), 10억 달러 이상의 평가로 인수된 경우도 거의 없습니다.
가장 성공한 스타트업 중 하나는 SolidWorks의 창업자가 2012년에 설립한 OnShape이며, 이 회사는 2019년에 PTC에 4억 7천만 달러에 매각되었습니다. 스타트업들은 이 공간의 각 수직 시장을 공략하려 하고 있지만, 아직 유니콘 지위에 도달한 곳은 없습니다.
기존 업체들의 해자는 매우 깊고 전환 비용은 매우 높은 위험을 수반하기 때문에 이 시장은 거의 침투할 수 없는 상태입니다. 하드웨어 조직은 위험 회피 성향이 강하며 새로운 기술을 흡수하는 속도가 낮기 때문에, 우리는 "생성형 AI" 기능이 대규모로 확장될 것이라고 생각하지 않습니다. 역사는 중견기업 및 기업 시장에 중점을 두지 않는 한 벤처 스케일이 가능한 회사를 구축하기 어렵다는 것을 보여줍니다. 그럼에도 불구하고, 우리는 특정 유망한 수직 시장이 있다고 믿습니다.
물리적 설계 소프트웨어의 미래는 어떻게 될까요?
이 도구들의 미래는 한 문장으로 요약할 수 있습니다: "클라우드 기반의 협업 도구와 증가하는 설계 자동화."
CAD와 같은 산업 설계 도구들은 모든 물리적 산업에 있어 매우 중요한 소프트웨어입니다 - Cadence의 칩 설계를 가능하게 하는 780억 달러 규모의 사업과 Dassault의 기계 부품 설계에서의 500억 달러 사업, Autodesk의 건설 모델링 도구에서의 540억 달러 사업까지. 지난 50년 동안 이들 도구는 기업에서 가장 높은 연간 계약 가치(ACV)를 차지했지만, 그동안 크게 변화하지 않았습니다.
우리는 생성형 AI 및 기타 기술적 혁신이 이전 비용의 일부로 고품질의 하드웨어 설계를 가능하게 하고, 하드웨어, 전기 및 기계 엔지니어들의 워크플로를 변화시킬 것이라고 믿습니다.
우리는 하드웨어와 복잡한 물리적 시스템을 설계하고 테스트하는 방식에서 패러다임의 전환이 초기 단계에 있다고 생각합니다. 특히, 앞으로 몇 년 동안 혁신을 볼 수 있는 네 가지 트렌드에 대해 기대하고 있습니다.
- 생성형 설계: 설계 소프트웨어에서 가장 흥미로운 트렌드는 생성형 설계입니다. 이 아이디어는 큰 잠재력을 가지고 있지만, 아직은 가치를 창출하지 못하고 있습니다. 토폴로지 최적화(생성형 설계)와 시뮬레이션이 더 나아지고 빨라지면서, 더 많은 엔지니어들이 부품 및 조립체를 자동 최적화하기 시작할 것으로 예상됩니다. Autodesk는 Bernini라는 3D 데이터를 학습한 기초 모델을 훈련했습니다. 이 모델이 "나에게 자동차를 설계해줘"라고 말하는 수준에 도달할 가능성은 거의 없지만, 간단한 브래킷, 못, 또는 개별 구성 요소는 생성형 모델을 사용하여 설계할 수 있을 것입니다. 이 분야에서 기술력이 높은 팀이 흥미로운 소프트웨어를 구축하고 산업을 앞당기는 데 기여할 기회가 있습니다.
- 시뮬레이션: 실제와 시뮬레이션 간의 간격이 좁아지고 있으며, AI 기반 시뮬레이션은 가장 흥미로운 연구 트렌드 중 하나입니다. AI 모델은 엔지니어링 팀이 기존 PDE 솔버 방법으로는 불가능한 속도, 깊이 및 폭으로 설계 공간을 탐색할 수 있게 할 것입니다. 코파일럿 기능도 시뮬레이션 워크플로를 변화시킬 수 있으며, 예를 들어 설정 자동화, 지오메트리 정리 등이 가능합니다. 이 분야의 기준은 매우 높으며, 엔지니어들은 오랫동안 잘못된 약속에 실망해 왔지만(예: 테스트 지오메트리가 학습 세트와 다를 때 나쁜 결과), 시간이 지남에 따라 결과와 워크플로가 개선될 것으로 기대합니다. 난류 데이터를 단순히 업스케일링할 수 있는 기회만으로도 하드웨어 팀에게는 엄청난 영향을 미칠 것입니다.
- 제조를 위한 설계: 혁신이 필요한 또 다른 영역은 제조를 위한 설계(또는 건설의 경우 시공성 검토)입니다. 이 과정은 설계를 검토하고, 제조 프로세스와 재료 가용성을 평가하며, 실제로 효과적으로 제조될 수 있는지 결정하는 과정입니다. 공급망의 디지털화는 설계 통합을 개선하여 더 일찍 제조 가능성을 판단할 수 있게 할 것입니다. 적층 제조가 계속 확장됨에 따라 새로운 DFM 플랫폼이 점점 더 중요해질 것입니다.
- 자동화된 물리적 설계 품질 보증: 현재 AI는 대량의 데이터를 요약하고 요청에서 맥락을 파악하며 이를 바탕으로 반복적인 프로세스를 자동화하는 데 능숙합니다. AI는 설계를 자동으로 평가하고, 제조 프로세스와 재료 가용성에서 얻은 데이터를 사용해 잠재적인 문제를 식별하고, 이를 바탕으로 최적화 권장 사항을 제시할 수 있어야 합니다.
물리적 설계는 소프트웨어에서 해자가 어떤 모습일 수 있는지에 대한 훌륭한 사례 연구를 제공하는 복잡한 공간입니다. 자동화와 수직화가 증가함에 따라 이 분야에는 오랫동안 미뤄져 왔던 많은 혁신이 이루어지고 있습니다.
Comments ()